The U.S.-China trade war: Here’s what it means for medical device industry suppliers
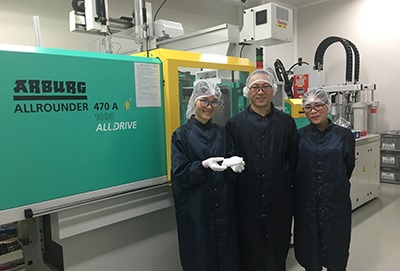
July 24, 2019 By Chris Newmarker
If the tariffs actually make a country great again, it might be Malaysia, Vietnam or Costa Rica, global medical device industry suppliers say.
[Image by art director Matt Claney]
The U.S.-China trade war is certainly affecting where U.S. medical device companies decide to make their products. But don’t expect a bunch of manufacturing to come back to the United States.
“They are looking at what I would call ‘right-shoring,’” Freudenberg Medical CEO Max Kley said of his company’s medtech customers. For 12 years, Freudenberg (Carpinteria, Calif.) has had a plant in Shenzhen, China, just outside Hong Kong, where about 150 workers are engaged in thermoplastic and silicone injection molding and assembly of finished devices.
With tariffs on both sides apparently here to stay, medical device customers are adjusting their supply chains, but it’s more about shifting manufacturing to other low-labor-cost locations such as Malaysia, Thailand, Vietnam, Costa Rica or Mexico, Kley told Medical Design & Outsourcing.
“It’s not necessarily moving them back to the United States,” Kley told us.
“What we are seeing is customers really looking at what they want to do with their supply chain,” said Charlie Mason, SVP of the medical division at Sanmina (San Jose, Calif.). “For next products, where do they want to be? And they’re doing that evaluation.” Sanmina has an FDA-registered facility in Kushnan, outside of Shanghai, that makes complex electromechanical assemblies for medical devices. (Another plant in Shenzhen meets the ISO 13485 standard but doesn’t presently ship to the U.S.)
“Customers are examining the next most competitive footprint that would make sense. So for us, we might look at India, or we might look at Malaysia, both FDA-registered locations. For our customers, it’s a matter of if they want to keep it in a particular region, go ahead and look at our alternative footprint,” Mason explained.
There was a time when medical device customers might ramp up in China without doing a full analysis, but those times are over, he added.
“Before customers make a decision, they’re evaluating what the impact is overall — on the total cost of ownership and the return on investment. If you’re going to change, you want to drive the most value that you can,” Mason said.
And the tariffs appear to be accelerating a shift that was already taking place.
“We’ve talked about Thailand and Malaysia and Vietnam more in my circles in the last two years than we talked about them in the prior 20,” said Mark Bonifacio, of Bonifacio Consulting Services (Natick, Mass.), who advises medical device companies looking to outsource manufacturing overseas.
A problem that isn’t going away
Haidi Li, Xingtie Deng and Shaohua Yin (left to right) are among the roughly 150 employees at Freudenberg Medical’s FDA-registered operation in Shenzhen, China. The Shenzhen plant manufactures medical components in silicone and thermoplastics. [Image courtesy of Freudenberg Medical]
Under President Donald Trump, tariffs have become a go-to negotiating tactic with other countries, including close U.S. allies such as Canada and the European Union. In late May, Trump threatened to levy them against Mexico over illegal immigration; had he followed through, it could have been a serious situation for the U.S. medtech industry as many companies increasingly manufacture south of the border.
But as of this writing in mid-July, perhaps no trade dispute appeared to be as deep and long-lasting as the confrontation between the world’s two largest economies.
The countries in June agreed to a truce to avoid additional tariffs, but duties on hundreds of billions of dollars worth of goods remain in place indefinitely. The U.S. medical device industry initially faced nearly $1 billion in tariffs after the Trump administration had Customs and Border Protection start collecting additional dues on goods imported from China in July 2018, trade group AdvaMed reported at the time.
In some ways, though, medical device companies are a bit lucky because they were later to the game than, say, consumer or electronics companies when it came to outsourcing manufacturing to countries with low labor costs such as China, according to Freudenberg’s Kley.
“That means that many of those decisions can still be made or can be made with a broader horizon than just cost,” he said.
Medical device companies have also had some success obtaining relief from U.S. tariffs on goods made in China. The U.S. in July exempted several categories of medical devices from the 25% tariffs, including surgical, radiotherapy and dental devices.
Medtech manufacturing in China is here to stay
Sanmina has an FDA-registered facility in Kushnan, outside Shanghai, that makes complex electromechanical assemblies for medical devices. [Image courtesy of Sanmina]
Despite the tariffs, a lot is going right when it comes to manufacturing medical devices in China, according to Bonifacio. Wage increases, dictated regionally by government authorities, have slowed down. Bonifacio has noted more favorable tax treatments for small business and manufacturers, and the Chinese government is encouraging the creation of new manufacturing locations — farther out from Shanghai, for example.
Bonifacio has found that the government’s push to teach English in schools has reduced the language barrier over the years, especially when he’s interacting with younger people. The infrastructure in China is impressive, and Chinese plants are rapidly expanding their use of robotics in manufacturing, he noted.
As Chinese companies create their own intellectual property, the government has become more serious about enforcing IP protections too, Bonifacio said. “They’ve absolutely gotten better. Anyone who does manufacturing in China will tell you that. Now are they perfect? No. But they have to make a government commitment to make sure that they improve on that.”
Medical device companies are also increasingly manufacturing in China for China, as the country’s middle class expands and demands higher-quality healthcare.
Mason at Sanmina has seen customers talking about pulling some products destined for the U.S. out of China — at the same time that they’re talking about ramping up manufacturing of products sold in China.
Kley at Freudenberg has also noticed a shift in the company’s Chinese production toward helping medtech companies create sophisticated devices destined for the local market.
“This is where we see the market opportunity, because that’s where many existing manufacturers in China do not have the technology, or they do not have the trained associates, and they don’t have the quality system to really cater to these demanding applications,” Kley said. “There is room to play at the top end, the more demanding end of the market.”
“If you are a multinational medical device player, I don’t think you can afford to miss out on the growth opportunities offered in China or the Asia Pacific medtech markets,” he said.
A case for reshoring?
Tariffs, however, are strengthening the case for manufacturing in the U.S., said Dennis Vetrano, sales & business development manager at Lockheed Martin’s Polaris Contract Manufacturing business (Marion, Mass.).
Polaris, which provides electronic contract manufacturing for medical and other industries, has seen some interest from a variety of customers about manufacturing more printed circuit boards in the U.S. versus overseas.
“I think some device manufacturers have found out the hard way, that the cost savings can come with multiple issues of which the most significant is a major delay in delivery, causing a halt in the products manufacturing,” Vetrano said.
Vetrano listed a host of reasons why it makes more sense than ever to make medical devices in the United States, including better IP protection, better control over external forces and less language barriers.
“There’s been a better understanding that medical device manufacturers need to take a better look at total cost of ownership in understanding the struggles that can go on by having the brains of your electronic device (PCB) produced elsewhere, out of the U.S.”