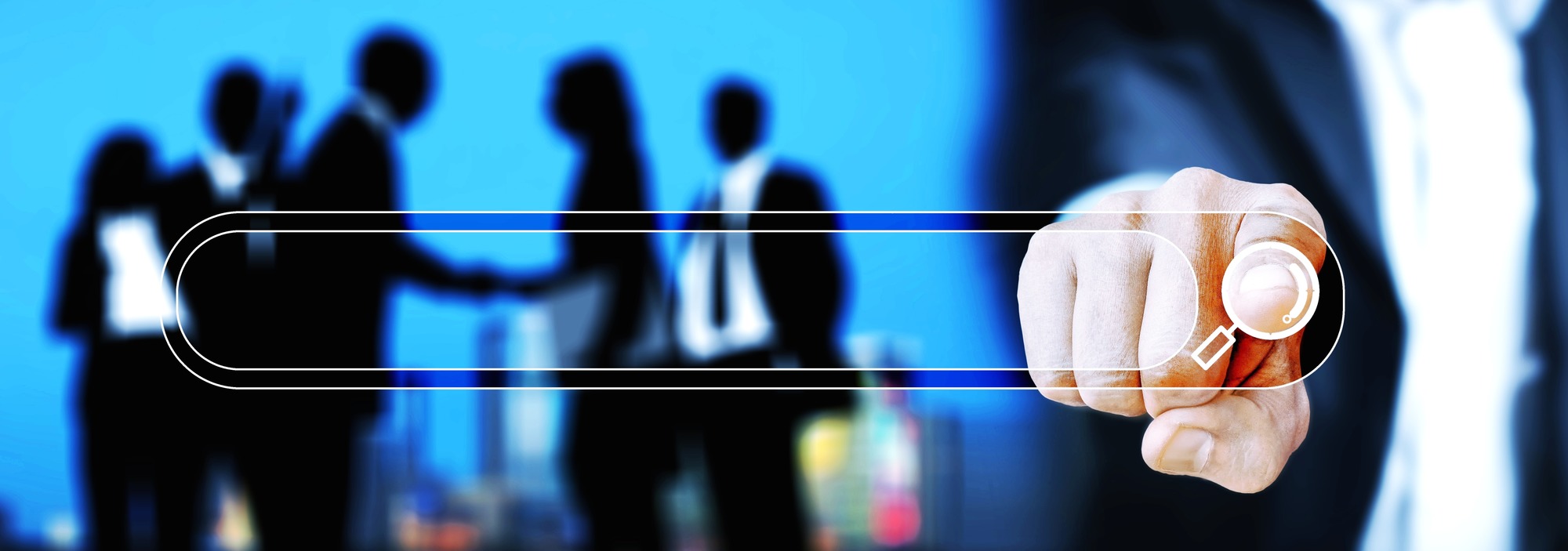
Businesses are constantly being tested by our competitors – either on price, quality of goods or service, or convenience. Any competitive edge might be the difference between a new customer and a lost sale.
Our procurement services help you streamline the entire product development cycle and to seek out innovative products or services to help get to market effectively. We offer a broad portfolio of services that help you obtain the information you require to make sound business decisions, optimize your supply chain, maintain end to end quality oversight and gain a competitive advantage. With the right procurement tools, enables them to improve upon the current procurement process is critical.
No matter how your products are catagorized into standard commodity items or cutting edge innovative design, we believe enhanced relationship with our business partners are essential to sustain a continued growth.
No matter anywhere you operate, our team of experts can develop an evaluation program to meet your needs…
To Know More About Our Processing Operations, Click Below >>
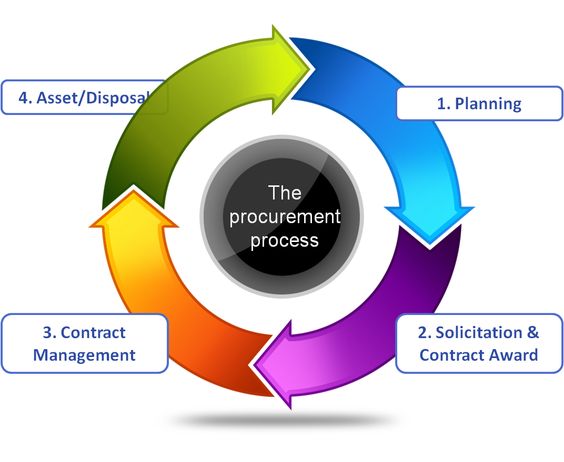
Our Procurement Process Steps and Details, click to review
-
Sourcing
Review the inquiry package and to follow up with customers, make sure all details are clarified prior to proceeding. Details may include:
- Product Specifications
- Quality Standards and Requirements
- Certification Compliance
- Packaging Standards
- Materials Usage and Availability, Materials Specifications
- Target Cost, if available
- Samples Availability
-
Conduct research with reference to particular industry standard, factory leadership, geographical nature, supplier distribution or pattern, market trend/movement, competitive positioning and others that related to the project.
-
Vendor Sourcing (web research, industrial seminars, trade magazines, trade shows, referrals, market research and others )
-
Sourcing for at least 5 potential vendors
-
Continue updating supplier information data sheet
-
Sampling – make samples in accordance with the requirements or to benchmark against customer’s samples
-
Vendor Evaluation – focus on pricing, engineering, product quality, follow up service
-
Vendor Review, Discussion and Negotiation
-
Supplier Selection
-
Contract and Agreement Compliance
-
Order Fulfillment, Vendor Management
-
Supplier Audit, Suplier Qualification, Supplier Rating
-
-
Continue to develop Supplier Alliance and Partnership
Factory Survey – focus on …
An extensive Factory Background Research
- Manufacturing Capability, Capacity & General Practices
- Overall Quality Concepts and Practices
- Examine Quality of Existing Products
- Export Practices, Existing Countries of Export
- General Manufacturing Lead Time
- Payment Terms
- Strength and Eagerness In Communication
- “Request for Information” Data Sheet (RFI) fill up and validate,
- Examine factory Quality Manual and QA documentation
- Examine entire Quality Systems throught In-Coming, In-Processing and Out-Going manufaturing stages
- ISO 9001 – Version 2000
- 5S QA System
- SA 8000 Social Accountability, Country Labor Law Compliance
- GMP Standard
- Six Sigma
- C-TPAT (Customs Trade Partnership Against Terrorism)
- PPAP – Production Part Approval Process
- FMEA – Failure Mode and Effect Analysis, etc.
Engineering and Product Development – focus on…
-
Preliminary product discussions – ideas, concepts…
-
Defining product specifications
-
Completion of engineering designs, drawing, defining specs, tolerance, etc.
-
Certificate and approval process follow up– ROHS, CE, UL, IEC, VDE, etc.
-
Convey entire customers’ requirements to vendors to make sure no misunderstanding
-
Cost and budgetary control
-
Timeline catch-up and proper scheduling putting in place
-
Prototype, model, tooling fabrication and sampling in process
-
Initial testing and product evaluation… debugging…
-
Product approval
-
Test market and necessary product improvement
-
Trial run…. final debugging….
-
Production run and monitoring
-
Follow up with necessary engineering changes and updates, (ECR, ECN.)
Quality Control/Quality Assurance – focus on…
-
Derive a complete Quality Plan and effectively implement it
-
Coordinate efforts and conduct in-coming, in-process & out-going quality management and inspection.
-
Set up and implement inspection system with effective inspection plan putting in place
- Internationally recognized sampling inspection plan i.e.., MIL Std. 105D – AQL, PPM and others
- Driving for continueous improvement in Quality Operating System (QOS) and Cost of Quality Systems (CQS)
- Help investigate defect findings with vendor after inspection
- Bring up strategic suggestions to drive continuous improvement on product quality, design upgrade and others
QA and Preshipment Inspection
- NGL liaise with vendor to request for notification of our inspection in 10 days prior to delivery.
- NGL’s inspector and QA team should be well familiar with product requirements before inspection. Need to clarify with customer pertaining to all requirements.
- NGL issue Inspection Report in 48 hours after passing inspection.
- When product rejection or product under pending stage happens, NGL needs to inform customer concerning cause, resolutions or to suggest for remedial or corrective action.
- NGL to update vendor rating, scorecards with respect to pricing, on-time delivery, quality, service.
Booking of Shipment
- NGL to book shipment from forwarder in 5 days prior to delivery.
- NGL to cancel booking in any case when product cannot be delivered on time. It happens like delay delivery, rejection during inspection or others events that retain product from delivering.
- Vendor to send cargo loading plan to NGL 3 days before delivery for NGL to submit to forwarder when cargos are delivered to container depot.
- NGL obtain shipping order release from forwarder.
- After vessel departure, forwarder submit 3/3 original Bill of Lading to NGL in 48 hours.
- Request forwarder for weekly/bi-weekly/monthly shipment reports
Continued Project Management
- Manage day-to-day operation for project planning, scheduling, engineering, order fulfillment, etc.
- Work under continuous basis:
- Vendor negotiation
- Payment term
- Improvement :
- Product design , quality upgrade
- Material substitution and upgrade
- Product consolidation, logistics efficiency.
- Keep appraised of :
- current economics
- business situation
- material shortage and cost fluctuation,
- Currency fluctuation
- Country labor law update
- Change of taxation system
- Sourcing infrastructure, geographical benefit
- Make recommendations to customer for improvement in product utility, cost, quality, delivery, etc.
- Achieve on-time delivery within specified shipping window
- Continue develop vendor database, perform vendor certification, develop supplier alliance and partnership
Plant Audit and Procurement Images
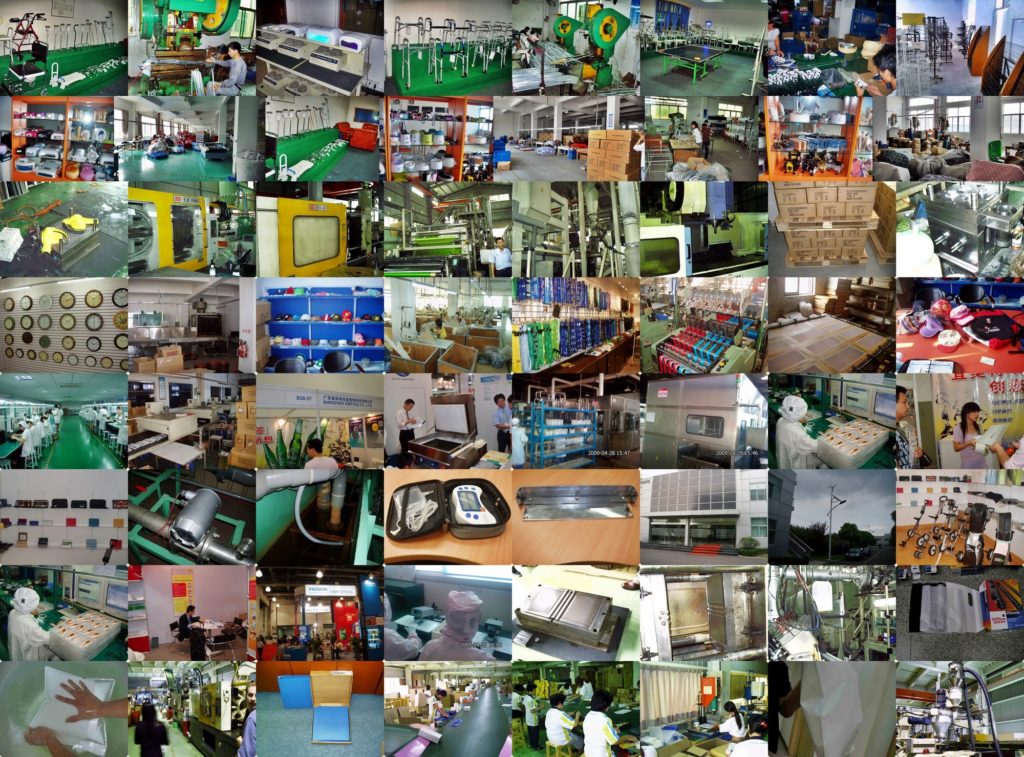